White Masterbatches
Of all the types of masterbatch used in plastics applications, a white masterbatch is the most commonly used. It gives the final product whiteness, brightness, and opacity. Various chemicals such as titanium dioxide and other pigments are used to produce a white masterbatch that gives plastic products high opacity, whiteness, and brightness.
Black Masterbatches
Carbon Black is primarily used as a black pigment due to its tinting ability, cost-effectiveness, and excellent results. For carbon black, the surface area is inversely proportional to particle size. In other words, the smaller the particle size, the greater the surface area. Carbon black pigments give high opacity, depth, and lustrous blackness to plastic products.
Additives Masterbatches
POLYTEC has invested in the development of new products. We are able to offer a wide variety of additives that improve the physical and chemical properties of polymers and masterbatches to meet customer needs during application. The process of becoming the final plastic product.
Oxo Bio Degradable Masterbatches
AddiFlex – Harnesses environmental forces such as heat, oxygen, and sunlight to mimic nature and cause biodegradable degradation. Addiflex is a visionary, easy-to-use, and safe solution to the plastic waste problem. It is an environmentally friendly system of additives and composites, and adding Addiflex to plastics has economic and environmental implications.
Colour Masterbatches
Colorants are used to create color masterbatches of different shades depending on the desired color and application. We have developed more than 10,000 shades according to customer requests. POLYTEC’s Color Matching Lab has state-of-the-art facilities to develop the colors of your choice.
We have developed over 10,000 color shades to meet customer requirements. POLYTEC have
state-of-the-art facilities in our color matching laboratory, which enables us to develop colors as per the choice of our customers .
Filler Masterbatches
Advantages;
A cost-saving solution to partially replace plastic resin, talc filler helps plastic companies reduce production costs, thereby improving the competitiveness of their products. Improved properties We do more than just provide our customers with cost-effective material solutions.
Improvement of Properties
• Improvement of heat resistance, stiffness, and rigidity of plastic materials
• Improvement of surface wear resistance and slip resistance of plastic materials
• Reduction of shrinkage rate of plastic materials, improvement of dimensional stability of finished products
• Improving printability
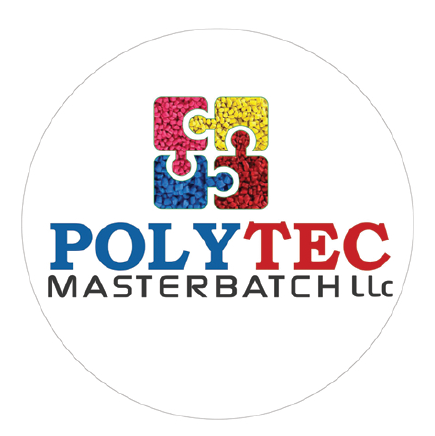